Dyeing Silk
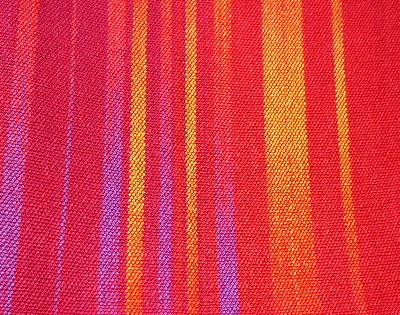
Dyeing silk is a two step process: de-gum, and then dye. I always assume silk comes to me with the sericin (gum) still in it. I remove it in an alkaline bath of water, detergent and soda ash, then I apply the dye.
Specifics? I use a table top roaster with inside dimensions of about 12" by 18" x 6" deep (or so, I'm guessing here). I fill it about 2" deep, squirt in some dish detergent and add 2T soda ash. Then I layer in the silk, about 2 to 3 ounces worth, turn it on to 215ºF and leave it for 2 to 3 hours. After de-gumming, I lift out the silk, drain it, and rinse out the pan.
I refill, with 2" water, add a cup of vinegar or 2T citric acid crystals, the dye stock, and then re-enter the silk. I leave it, at 215ºF, for another 2 to 3 hours. I let the silk cool in the dyebath, and the next day I rinse and dry it. I use up existing dyestock solutions, either Lanaset or Cibacron fiber reactive. In fact, the only dye I won't use on silk is *weak acid* or level acid dyes, sometimes called Kiton type.
And because it's all about the photos:
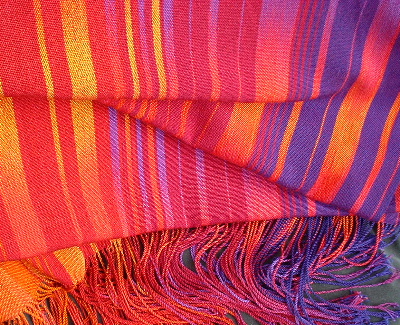
Treenway's 8/2 reeled silk sett at 24 epi. Dyed as yarn, not fiber, some painted and some immersion, as described above.